- Purpose
The purpose of this guide is to describe in detail and in a simple way how to improve processes by using one of the basic LEAN tools. This tool can be applied on various kind of processes like: production, logistic, engineering, office work, financial and so on. There is not any limitation to apply this tool.
- A Process
Our daily activities are built from processes, where each one of us is taking a part in the process. In each process there are suppliers that supply the inputs for the process, and the customers that receive the output from the process.
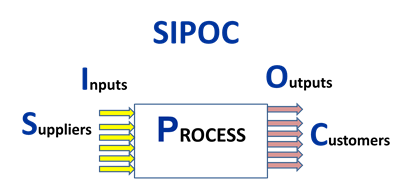
The process improvement is done by workshop and divided into steps, with each step based on the output result of the previous steps. This workshop usually lasts from half a day to two days depend on the complexity of the process.
- Workshop Preparation
- Select the process to be improved, its goals and the required improvement, reducing process Lead-Time. Identify the suppliers who initiate the process, and their inputs to the process
- Identify the suppliers who initiate the process, and their inputs to the process
- Identify the customers who receive the output of the process.
- Identify the current process Lead-Time , and the required Lead-Time after the improvement.
- Identify all the disciplines and entities that participate in the process. Invite those people to the workshop.
- The Office Supplies needed for the workshop:
- A blank sheet of paper, about 400 cm long and 90 cm high.
- Square Post-it notes or similar notes in different colors
- Round small post-it notes in red and green color
- Markers in different colors
- Preparation ) It is done before the workshop itself)
- Place on the wall the sheet of paper
- On the X axis marks lines at intervals of a sticker
- On the Y axis on the left side, stick different color post-it notes for each of the process participant.
- It should look like this:
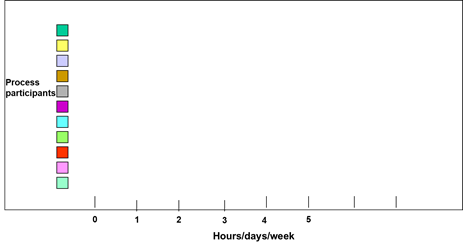
- Workshop facilitation
Step 1 – initiation
- Each of the participant describe his role in the process
- Short explanation of the workshop process
- On the Y axis post-it notes, write each discipline that participate in the process in different post-it.
- On the X axis, mark the time scale, (hours, days, weeks, month), depends on the process duration.
Step 2 – process mapping – document reality
- The process mapping is done in “swim lane” technic where all the activities of each participant in the process is maps on the same axil (at different color), on the time scale when it performs according the current activities in the process
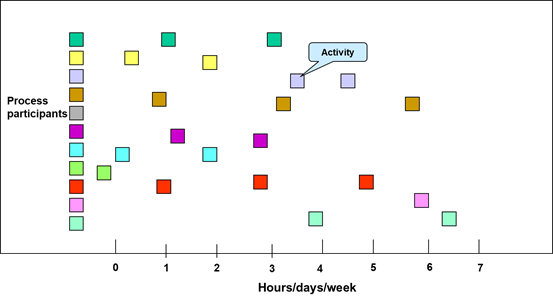
- The workshop participants describe the activity they are doing in the process, and this activity is written on the colored notes. Each stage of the process must be researched and documented, including the waiting time, so that at the end, a true and realistic mapping of the end-to-end process is obtained. Most of the time it is the first time everybody see the full process end to end.
Step 3 – Identifying waste in the process
Once the process mapping is complete, define the types of waste and added value in the process.
- Activities that the customer is not willing to pay for
- Activities that do not change the product or the information
- Activities that are not performed for the first time
- If one of the above criteria is obtain, the activity is considered as waste
If one of the above criteria is obtain, the activity is considered as waste
Added value definition
- Activities that the customer is willing to pay for
- Activities that change the product or the information
- Activities that are performed for the first time
All of the above criteria must obtain in order to defined as consider as added value
challenge and examine each one of the activities, classify it into added value – green circle, and waste – red circle.
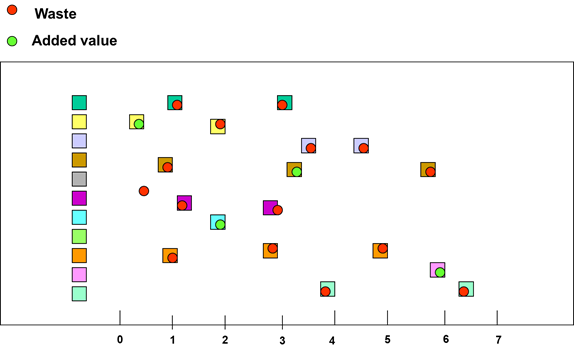
Step 4 Finding Opportunities for Improvement
After identifying all the wastes in the process, a structured brainstorming session is done on each waste and waste separately, (activity with a red circle). The purpose is to come up with ideas how to eliminate the waste. Each of the ideas is documented in a “to do list” format in the column of problems and opportunities. All the ideas must be documented
Step 5 Decision on corrective actions
Examine each idea and idea and decide what corrective actions has to be taken to reduce the waste. Also assign people to perform the corrective action and deadline for completion.
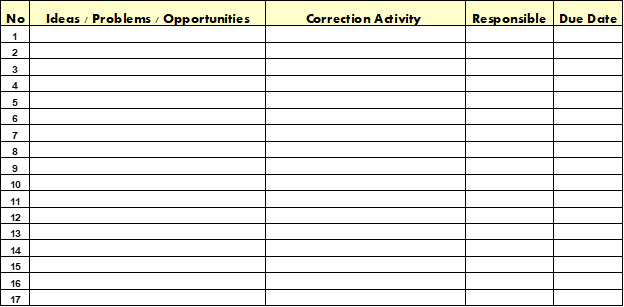
Step 5 Mapping the New Process
Build a new process assuming all the actions item in the do list has been completed, and the wastes had eliminated. In this mapping, most wastes are usually eliminated, so the process Lead-time should be reduced by tens percentage.
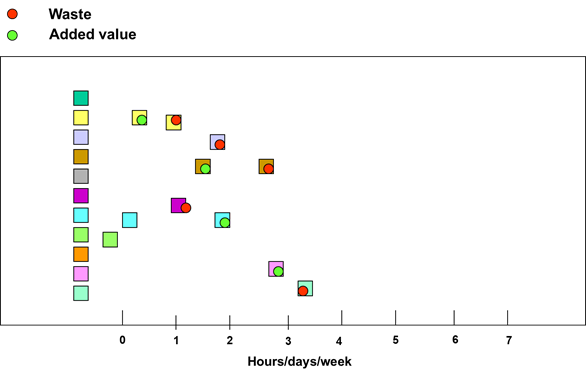
Summery
The end product of this workshop is a map of improved process and a list of action item to be done in order to reach the improved process. From this phase, action should be taken to execute the action items from the TO-DO list. This can take from few days to a few weeks. The goal is to finish the operations as quickly as possible.